Introduction to Hot Forming Techniques
Hot forming encompasses a range of primary methods, including extrusion, drawing, forging, and rolling. Among these, rolling stands out as the most widely employed forming process, albeit with some inherent limitations. Rolling is predominantly divided into three key sub-categories: flat rolling, shape rolling (employing specially designed roll grooves), and pipe rolling (incorporating the piercing process). Within the domain of forging, various sub-categorizations exist, such as hammering and pressing.
Forging can be executed under various conditions, including hammers, mechanical presses, up setters, or through a method known as roll forging. Pressing typically involves the creation of forged articles using hydraulic presses. Extrusion, on the other hand, often takes place in hydraulic presses that exert force to push hot steel through a die. Rolling operations occur in diverse types of rolling mills.
Hot working, or metal forming at elevated temperatures, serves two primary purposes: to reduce the resistance of steel to deformation, thus minimizing forming loads, and to cultivate preferred metallurgical structures that enhance the strength and ductility of the final products.
The most suitable manufacturing method for a specific product is determined by considering factors such as its material composition, dimensions, shape, intended usage, adherence to standards, and other relevant properties.
Numerous processes are available for the manufacturing of butt weld fittings, with several examples outlined below.
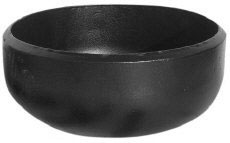
Cap Manufacturing Using Deep Drawing
Deep drawing stands as one of the most prevalent manufacturing techniques for caps. This method involves cutting a circular plate and shaping it through a deep drawing process.
Deep drawing, in essence, is the manufacturing procedure that transforms sheet metal stock, referred to as blanks, into shapes—whether geometric or irregular—where the depth exceeds half their diameters. The deep drawing process entails stretching the metal blank around a plug and subsequently maneuvering it into a shaping tool known as a die.
To achieve diverse shapes, a drawing press is employed to form sheet metal, and the final configuration is contingent upon the depth to which the blanks are pushed down. It is imperative that the metal used in deep drawing possess qualities such as malleability and resilience to withstand stress and tension-induced damage.
Step : 1
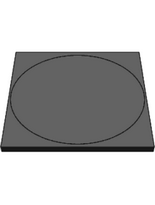
Step : 2
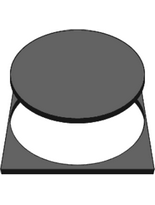
Step : 3
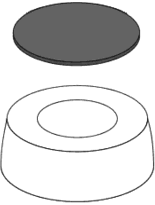
Step : 4
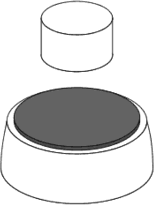
Step : 5
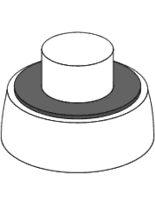
Step : 6
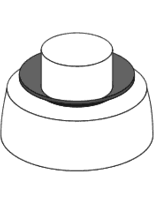
Step : 7
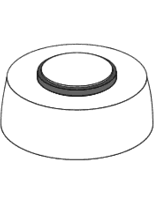
step : 8
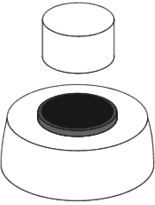
Result
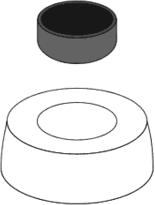
All the steps mentioned above give a brief explanation (the basic principle) about Hot forming, deep drawing method. Many more steps are needed, but hopefully the pictures give a good description.