Introduction to Hot Forming Techniques
Hot forming encompasses a range of essential methods for shaping metals at elevated temperatures, each serving distinct purposes in the manufacturing industry. The primary techniques of hot working include extrusion, drawing, forging, and rolling. Among these, rolling stands out as the most widely employed method, although certain limitations may apply. Rolling can be further classified into three major sub-categories: flat rolling, shape rolling (utilizing specially designed roll grooves), and pipe rolling (including the piercing process). Forging, another significant hot working method, can be subdivided into techniques such as hamming and pressing, among others. Notably, forging can be executed under various conditions, including hammers, mechanical presses, upsetters, and roll forging.
Pressing, a specific sub-process within forging, involves the production of forged components using hydraulic presses. Extrusion, on the other hand, typically utilizes hydraulic presses to drive hot steel through a die, shaping it into the desired form. Rolling, the final major hot-forming method, is carried out in diverse types of rolling mills.
The primary objectives behind conducting metal forming at elevated temperatures, commonly referred to as hot working, are twofold. Firstly, it serves to reduce the forming loads by decreasing the steel’s resistance to deformation. Secondly, hot working aims to establish preferred metallurgical structures within the material, optimizing the strength and ductility of the final products.
Selecting the most suitable manufacturing method for a given product is contingent upon various factors, including the material’s characteristics, dimensions, shape, intended use, adherence to industry standards, and other pertinent properties.
In the realm of manufacturing butt weld fittings, there exists a plethora of processes, with several examples outlined below.
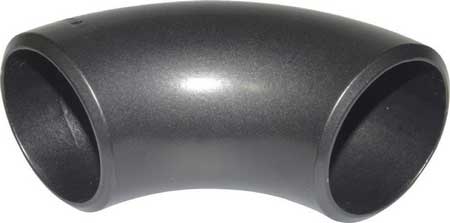
Elbow Manufacturing Using the Mandrel Method in Hot Forming
The mandrel method is a widely employed technique for crafting elbows from pipes, representing one of the most prevalent approaches in elbow manufacturing. In this method, the initial step involves heating the raw material, after which it is meticulously guided over a specialized die known as the “mandrel.” This unique process allows the pipe to simultaneously expand and bend to form the desired elbow shape. Notably, the mandrel method exhibits versatility, accommodating a broad range of pipe sizes.
Elbows fashioned from steel pipe joints play a pivotal role in industrial plants and are primarily produced through the hot mandrel bending process, starting from straight steel pipe stock. This method entails the manipulation of pipes at elevated temperatures, achieved by a combination of pushing, expanding, and bending operations, all facilitated by the inner tool, the mandrel itself. The specific characteristics of mandrel bending hinge on the integrated shape and dimensions of the mandrel being employed.
Elbows crafted using the hot mandrel bending technique offer distinct advantages over alternative bending methods. Notably, they exhibit minimal thickness deviation and can achieve shorter bending radii, making them a preferred choice for many applications.
Step : 1
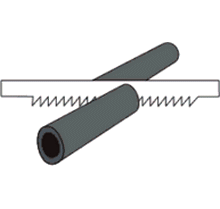
Step : 2
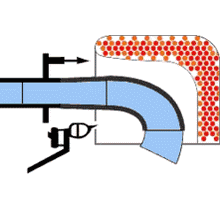
Step : 3
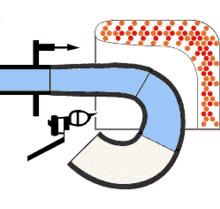
Step : 4
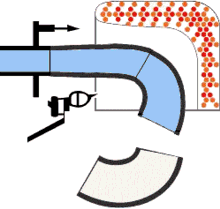
Step : 5
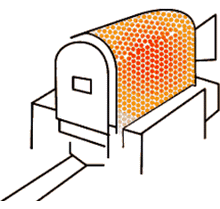
Step : 6
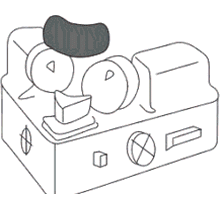
Step : 7
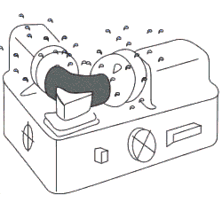
Result
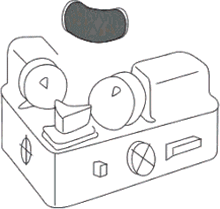
All the steps mentioned above give a brief explanation (the basic principle) about Hot forming, extrusion method. Many more steps are needed, but hopefully the pictures give a good description.