What is Induction Bending..
Induction Bending is a precise technique employed to curve pipes by applying controlled localized heating using high-frequency induced electrical power.
Initially designed for surface hardening of steel, the application of induction technology in pipe bending involves wrapping an induction coil around the target pipe. This coil heats a narrow, circumferential segment of the pipe to a temperature ranging from 850 to 1100 degrees Celsius, depending on the material being shaped. Once the optimal bending temperature is achieved, the pipe is gradually passed through the induction coil, all the while subject to bending force applied by a stationary radius arm arrangement.
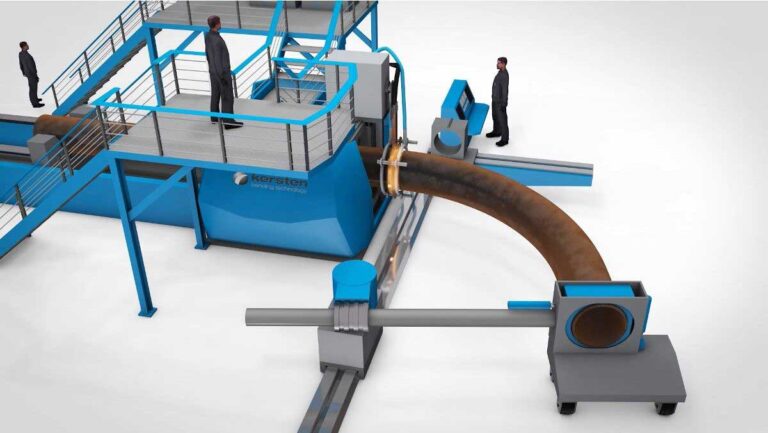
The Manufacturing Process of Induction Bends
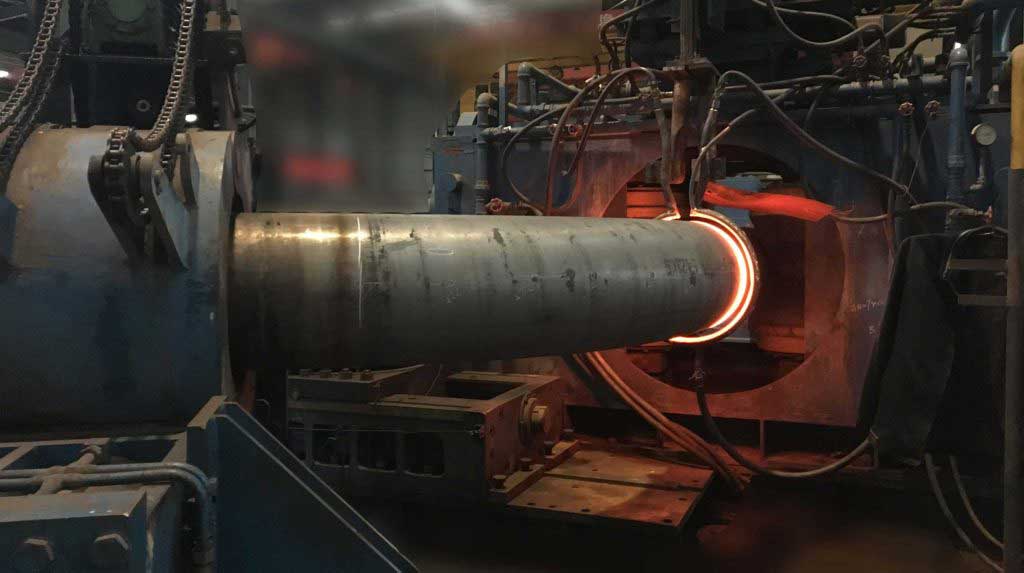
Induction bends are crafted within a manufacturing facility by guiding a straight pipe through an induction bending machine. This machine employs an induction coil to selectively heat a narrow section of the pipe material. The leading end of the pipe is secured to a pivot arm.
As the pipe advances through the machine, it gradually takes on the desired curvature radius. The heated section of the pipe, just beyond the induction coil, is swiftly cooled with a water spray on its external surface. This cooling process is vital because the unheated portions of the pipe on either side restrict the thermal expansion, resulting in diameter reduction as it cools.
Typically, most induction bends are fabricated with straight tangent ends that remain unaffected by the induction bending process. To connect these bends to other sections of pipe, field welds are made or pipe pup sections are attached to the unaffected tangent ends, allowing for a fitting process similar to joining straight pipe sections.
Induction bends are available in standard bend angles (e.g., 45°, 90°, etc.) or can be custom-made to specific bend angles. Additionally, compound bends (out-of-plane bends within a single pipe joint) can be manufactured. The bend radius is specified as a function of the pipe’s nominal diameter; for instance, common bend radii for induction bends include 3D, 5D, and 7D, where “D” represents the nominal pipe diameter.
Benefits of Induction Bends
- Enhanced Fluid Flow: Induction bends offer large radii, ensuring a smoother flow of fluids.
- Cost Efficiency: Utilizing straight materials is more economical than standard components like elbows. Induction bends can also be produced more quickly than welded standard components.
- Reduced Friction and Energy Consumption: Induction bends can replace elbows in suitable applications, leading to reduced friction, wear, and lower pump energy consumption.
- Minimized Welding: Induction bending decreases the number of welds in a system by eliminating critical point welds (tangents). This enhances the system’s ability to withstand pressure and stress.
- Strength and Uniformity: Induction bends exhibit greater strength compared to elbows, with uniform wall thickness.
- Lower Testing Costs: The reduced need for non-destructive weld testing, such as X-ray examinations, leads to cost savings.
- Inventory Reduction: Stocking fewer elbows and standard bends is possible when utilizing induction bends, streamlining inventory management.
- Faster Material Access: Straight pipes are more readily available than elbows or standard components, and the production of bends is typically faster and more cost-effective.
- Minimal Tooling: Induction bending requires fewer tools compared to cold bending methods, eliminating the need for thorns or mandrels.
- Environmentally Friendly: Induction bending is a clean process that eliminates the need for lubrication and recycles water used for cooling.
ASME B16.49
The scope of this standard primarily encompasses induction bends designed for use in transportation and distribution piping applications, such as those outlined in ASME B31.4, B31.8, and B31.11. It is important to note that process and power piping involve distinct requirements and utilize different materials that may not align with the limitations and examinations detailed within this Standard. As a result, process and power piping are not covered by this standard.